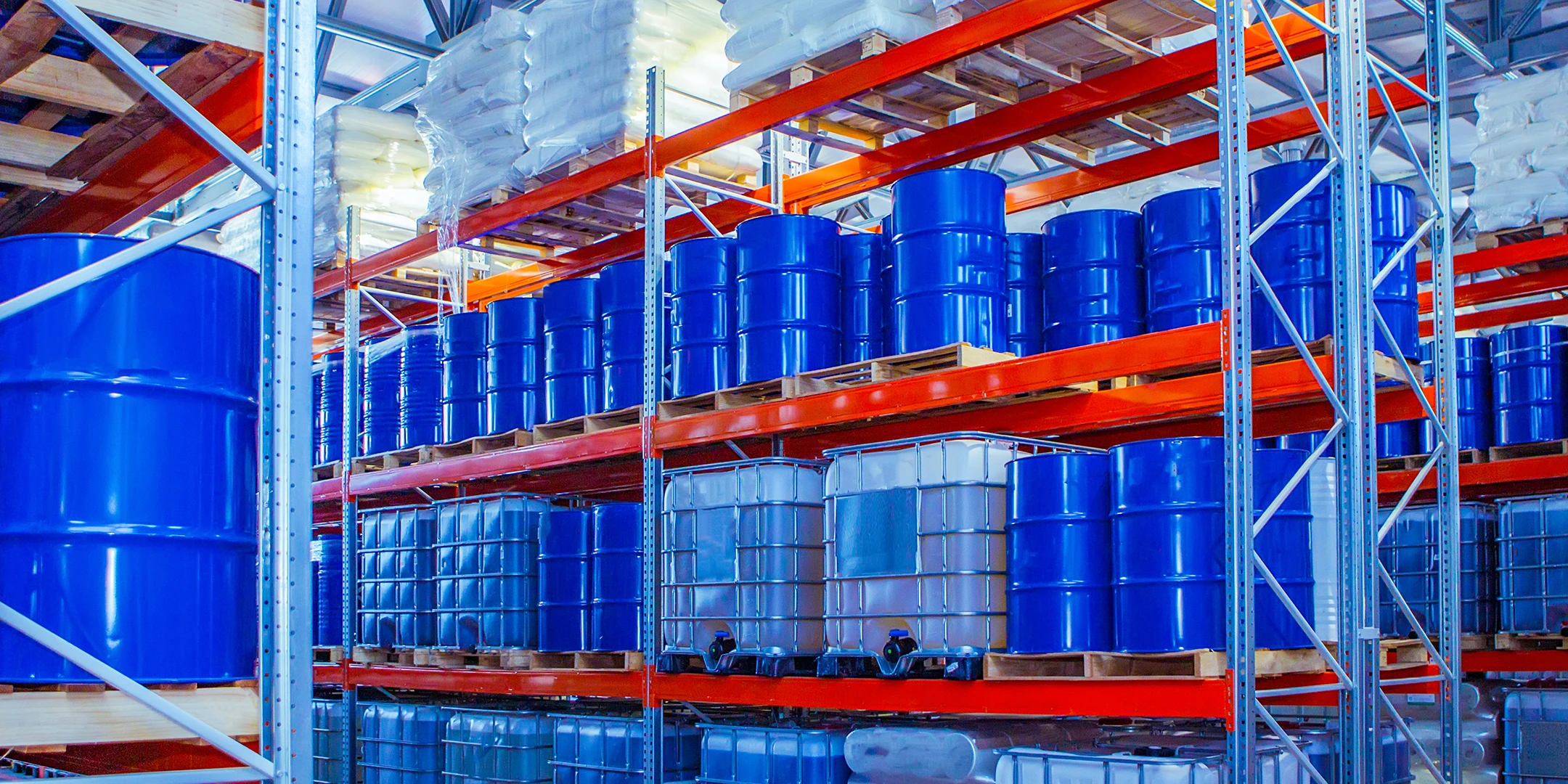
Your guide to the safe storage of hazardous substances
If hazardous substances are used in your company, they must usually also be stored. However, improper storage is often associated with significant risks to safety and health, especially when it comes to substances such as paints, varnishes, chemicals, acids, alkalis, solvents, or lubricants. Therefore, it is important to store hazardous substances in a way that protects both employees and the environment. Therefore, the safe storage of hazardous substances is a top priority.
Below, you will find out the basics about regulations, protective measures, and the digital organization of hazardous substance storage in your company. For further information on implementing a software solution for hazardous substance management in your company, read our free ebook!
The big book of digital HSQE management
Find out in detail how a comprehensive software solution can support you in the area of HSQE!
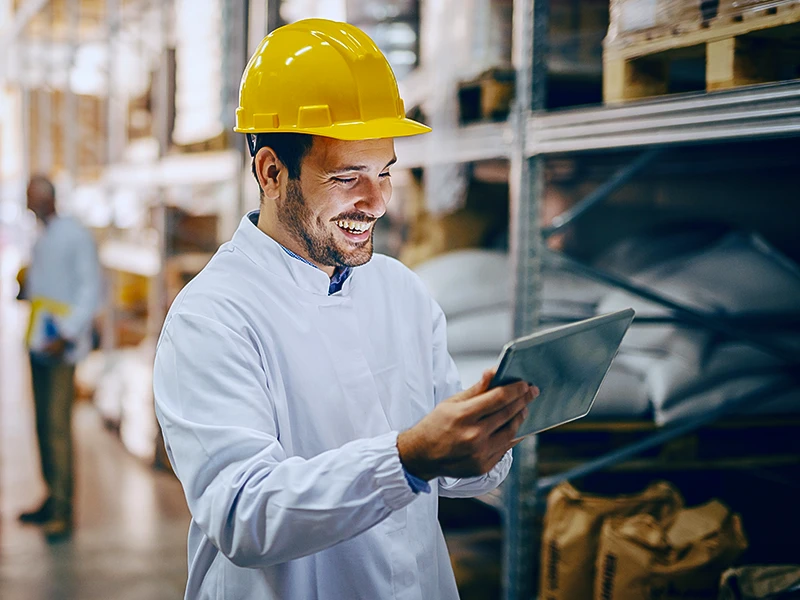
Basics of storing hazardous substances
If you work with hazardous substances in your company, you should exercise particular caution. This applies to all activities involving hazardous substances, including their use, transport and proper storage.
Basically, you have to differentiate between actual storage and provision. Provision means keeping hazardous substances for immediate use. Storing, however, means keeping them for later use or disposal.
Of course, you must always identify and evaluate all potential risks that arise from storing hazardous substances. This is done via the hazard assessment in your company, in which you identify possible sources of danger for your employees. Suitable protective measures must then be derived.
Protective measures for the safe storage of hazardous substances
In order to protect your employees from potentially dangerous situations, preventive measures are essential. We have compiled a selection of important guidelines for you below:
Joint storage of hazardous substances
Storing hazardous substances without an organization system is prohibited simply because it can lead to unintended and dangerous reactions between them. Certain hazardous substances must, therefore, not be stored together. This rule applies, for example, to flammable or combustible liquids in combination with oxidizing substances. In such cases, you can achieve safe storage by keeping substances with incompatible properties in separate rooms or ensuring sufficient safety distances in the storage areas.
The hazardous substances regulations clarify which substances you must store together or separately. In these, hazardous substances are assigned to so-called storage classes based on their hazard level. The class descriptions are based on the classifications according to the CLP regulation (Classification, Labelling and Packaging). Accordingly, you can store substances that belong to the same storage class together without problems. Different classes, however, must be kept separate.
Joint storage tables help you keep track of all hazardous substance combinations when storing them together. They show for each substance whether it is possible to store it together with other storage classes or whether joint storage is prohibited. Traffic light colours are generally used for labelling.
Organise the storage of your hazardous substances digitally
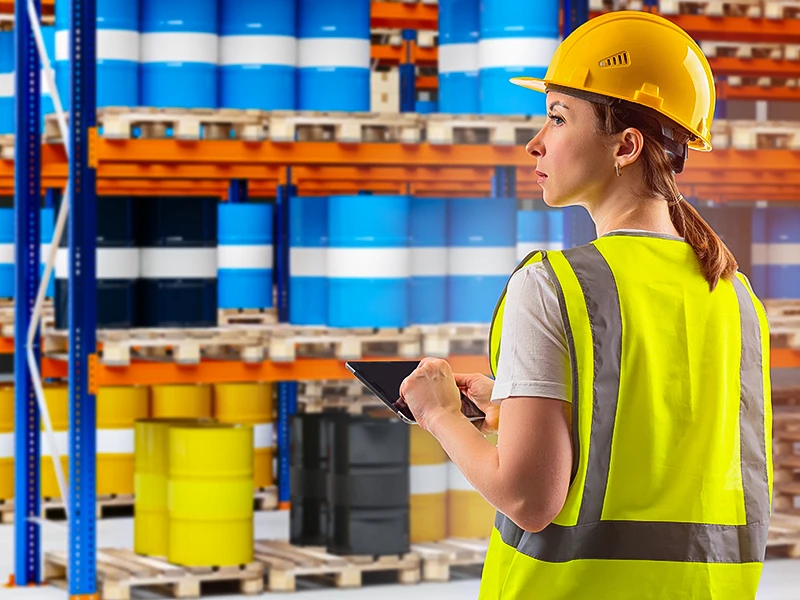
First, you can create an electronic hazardous substances register in which you note the material properties, storage location, and quantity. You then check the joint storage of selected materials directly in the system. iManSys tells you whether you can store the hazardous materials to be checked together, separately, or only to a limited extent.
Once the hazardous substances have been assigned to the relevant storage class, the joint storage of the classes can also be checked using the integrated joint storage table. It is also possible to check whether hazardous substances are being stored together in different locations.
With iManSys, you can organize not only the efficient and safe storage of hazardous materials but also the entire management of hazardous materials. Store safety data sheets on the dangerous properties of all hazardous materials. Also, consider the hazardous materials used in your hazard assessment, which can be created in the software. In addition, you can also fill out operating instructions for storing and retrieving as well as emptying and transferring directly electronically and then exporting them.
A software solution offers a holistic basis for the systematic development of your hazardous materials management system. You can find out how to do this step by step in our topic-related ebook. You can download it here free of charge:
The big book of digital HSQE management
Find out in detail how a comprehensive software solution can support you in the area of HSQE!
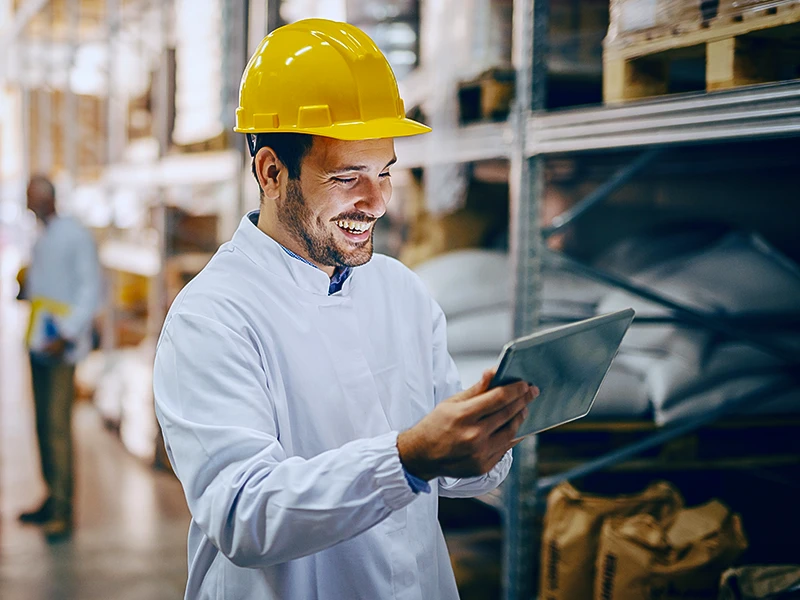
Share this post:
More blog posts
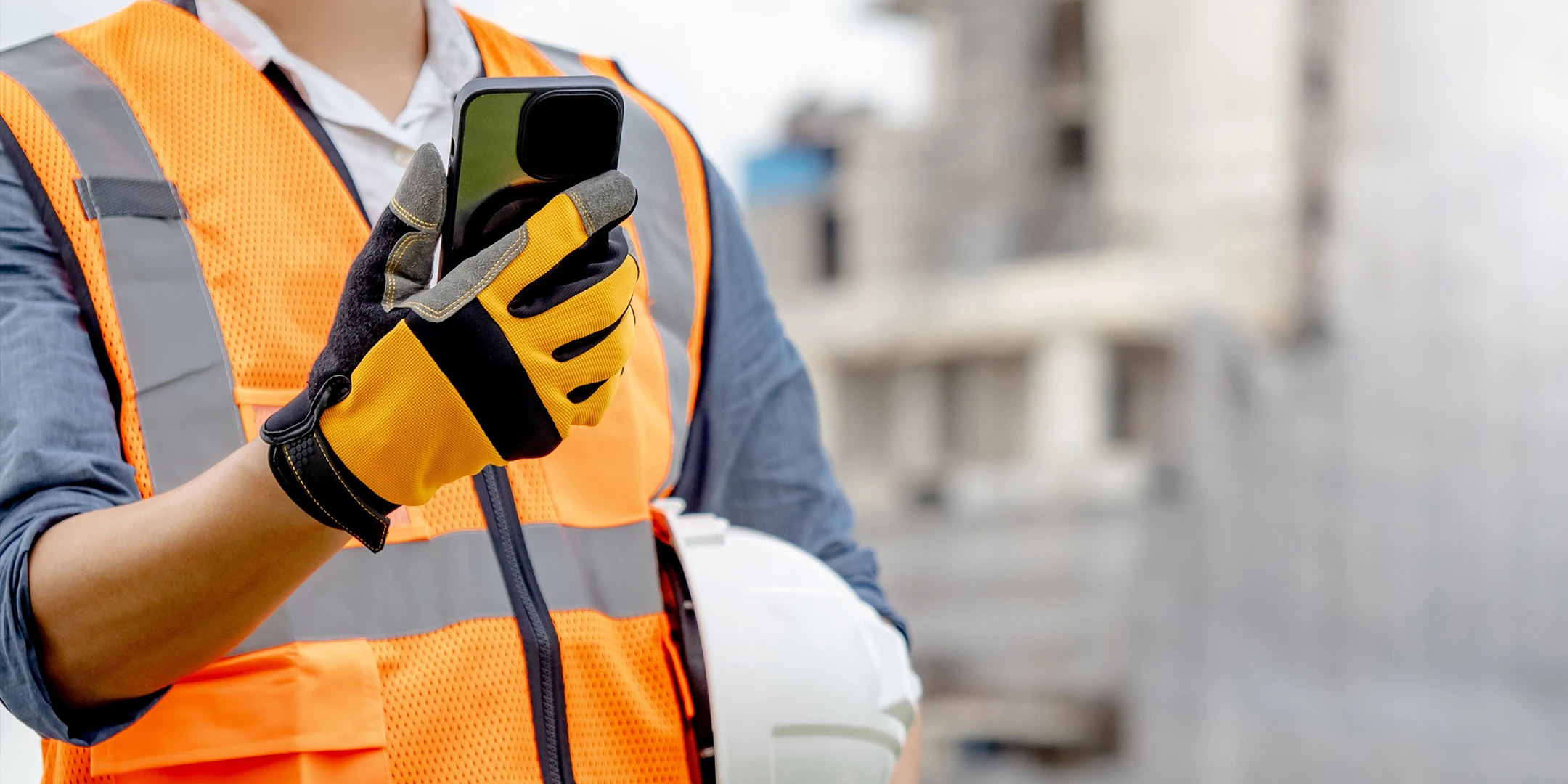
Mobile Occupational Safety
What’s the first thing that comes to mind when you hear the term “occupational safety” ? Perhaps personal protective equipment, specifically a hard hat. Or risk assessments, training, company guidelines. […]
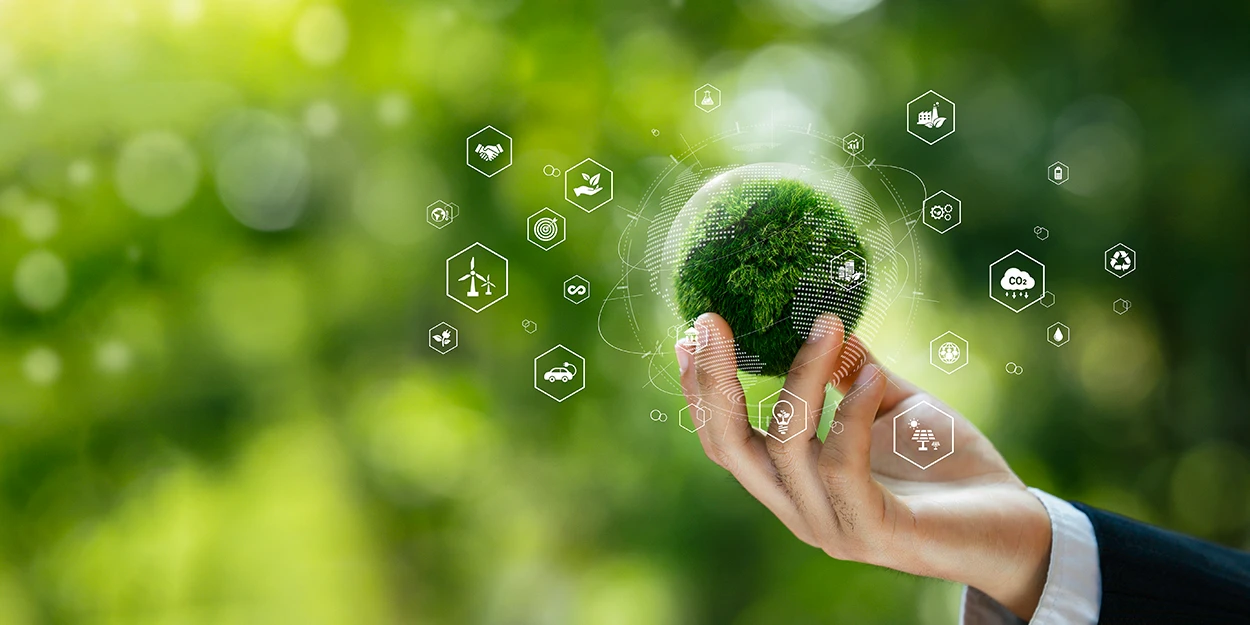
The key to sustainable success
Companies throughout Germany must gradually deal more intensively with the three letters ESG: Environmental Social Governance. Pursuing sustainability goals not only has a positive impact on the environment but is […]
Leave a Reply